|
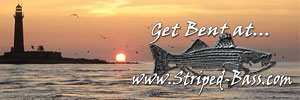 |
|
|
|
 |
|
 |
|
Plug Building - Got Wood? Got Plug? |
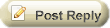 |
12-17-2007, 09:07 PM
|
#1
|
Primate
Join Date: Nov 2004
Location: Central Jersey
Posts: 106
|
Wood species question
I'm getting tired of a high percentage of my maple plugs splitting and was wondering if there are any other woods out there with the same density that aren't as prone to splitting? I use the BLO/spirits method of sealing and I've even tried soaking a batch for a few days and some of them still split so I'm pretty sure it's not that I'm not sealing them well enough. I was reading on a muskie site that others have had problems with maple splitting too, something to do with it expanding/contracting more than other woods.
Anybody got any ideas on different woods or possibly different sealers? I am open to suggestions(except Val-oil, I can't find it around here).
|
|
|
|
12-17-2007, 10:58 PM
|
#2
|
Registered User
Join Date: Feb 2005
Location: Burlington
Posts: 2,290
|
Val Oil - Home Depot has it. ask for it as it is not easy to find. Usually in the same area as Tung oil. Maple and Birch are prone to splitting, especially if the plug is not drilled thru the grain properly or if the grommet is pressed too tight for the belly hook. 
|
low & slow 37
|
|
|
12-18-2007, 02:09 PM
|
#3
|
Super Moderator
Join Date: Aug 2000
Location: Middleboro MA
Posts: 17,126
|
hardwoods are difficult for penetration of sealers. Maybe try CPES
maybe try air dried birch with a better sealer. tung oil is good.
heat up the wood and use epoxy, thin epoxy.
it's a difficult process.
|
|
|
|
12-20-2007, 05:16 PM
|
#4
|
Registered User
Join Date: Jan 2005
Location: Monmouth Co, NJ
Posts: 90
|
I do the epoxy thing on all my plugs including maple darters. It is a bit messy and good epoxy aint cheap, but no splittage yet.
Another benefit to doing the heat treat epoxy thing is that the plugs are dry and ready for primer in a matter of hours instead of days or weeks plus they stand up to the most dedicated bluefish attack.
Digger
|
|
|
|
12-20-2007, 11:10 PM
|
#5
|
Professional dumba$$
Join Date: Sep 2005
Location: New Bedford Ma
Posts: 541
|
I had issues with maple, cpes has solved most of the splitting, but you need a few coats. My first few batches didn't get sealed well enough with one application, and to my great embarassment, split.
|
|
|
|
12-23-2007, 09:31 PM
|
#6
|
Primate
Join Date: Nov 2004
Location: Central Jersey
Posts: 106
|
I have about a gallon and then some of watery thin(as compared to e-tex or devcon) boat building epoxy and an oven to heat the blanks. Would that work?
I have a few questions for you guys that do the epoxy thing. The big one is how do you coat the outside AND the throughhole and still have a way to hang it to cure? The other question is do you just use a bunch of epoxy and spin it like you would for a finish coat or do you try and get as thin a coat as possible? Also, could I use the boat building epoxy for a finish coat too, or am I better off sticking to e-tex and devcon?
I know I'm asking a lot of questions and I should just experiment but it can't hurt to get some advice from folks that have done it before.
|
|
|
|
12-23-2007, 09:44 PM
|
#7
|
Registered Grandpa
Join Date: Nov 2003
Location: east coast
Posts: 8,592
|
The cpes is the thinnest of the epoxies i know of, the boat epoxies are a little heavier but heating before mixing may help.
The inside coating is the reason for using thin as it works itself down the thru hole and belly holes. you can use a foam brush to take off the excess dripping and coat the outside. Use a pipe cleaner soaked in epoxy to run thru the holes to be sure the inside is covered.
You can put stainless steel screws on an angle over your bench and hang the belly holes of the plug on them to dry.
If you have a gallon of the boat epoxy it would sure be worth a try as a clear coat.
Hopes this helps.
|
" Choose Life "
|
|
|
12-25-2007, 12:53 PM
|
#8
|
Registered Grandpa
Join Date: Nov 2003
Location: east coast
Posts: 8,592
|
Forgot to mention,  , cut pieces of plastic straw and place them over the screws before drying the plugs.
Epoxy won't stick to plastic straws.
Got that one from Capesams, thanks CS. 
|
" Choose Life "
|
|
|
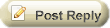 |
Thread Tools |
|
Display Modes |
Rate This Thread |
Linear Mode
|
|
Posting Rules
|
You may not post new threads
You may not post replies
You may not post attachments
You may not edit your posts
HTML code is Off
|
|
|
All times are GMT -5. The time now is 06:44 AM.
|
| |