|
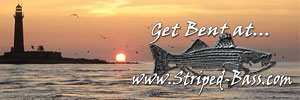 |
|
|
|
 |
|
 |
|
How To and Favorite Plug Forum Guides This location is for Plug Forum How-To and Step by Step guides as well as popular informational threads |
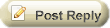 |
|
03-11-2005, 06:27 PM
|
#1
|
Uncle Remus
Join Date: Mar 2003
Location: Lakeville Ma.
Posts: 14,773
|
Duplicator How to
Well here goes nutin. Here are some photos of my duplicator and accessories. I know that I made it out of aluminum and used my machine shop trade but you can do just as good a job with hardwoods, table saw, dado blade, and drill press as long as you take your time and plan. There are a few things that are important in the design and I will mention them as I go. Hopefully you can use the photo's to help build your own. There are many ways to make a duplicator and mine is not an end all but I think this design is very simple and fairly inexpensive and best of all it works. I looked at several design's and incorporated all the things I liked about them into mine. Here goes. Paul
Last edited by ProfessorM; 03-12-2005 at 12:22 PM..
|
|
|
|
03-11-2005, 06:30 PM
|
#2
|
Uncle Remus
Join Date: Mar 2003
Location: Lakeville Ma.
Posts: 14,773
|
The duplicator
|
|
|
|
03-11-2005, 06:31 PM
|
#3
|
Uncle Remus
Join Date: Mar 2003
Location: Lakeville Ma.
Posts: 14,773
|
The mounting plate. I am sure you could use Corian, formica countertop, butcherblock, anything flat and stable should work good. A piece of aluminum that size at 1/2 inch thick should run you around 50 bucks. To me that is the way to go.
Last edited by ProfessorM; 03-12-2005 at 11:04 AM..
|
|
|
|
03-11-2005, 06:33 PM
|
#4
|
Uncle Remus
Join Date: Mar 2003
Location: Lakeville Ma.
Posts: 14,773
|
Sideview showing tool follower up against template
|
|
|
|
03-11-2005, 06:34 PM
|
#5
|
Uncle Remus
Join Date: Mar 2003
Location: Lakeville Ma.
Posts: 14,773
|
Template mounted on template holder. You have lots of adjustments. Plus you can always move the mounting plate if you want to make larger plugs. When you drill the template to mount on your template holder use a universal distance for all templates. The holes can be a little sloppy because you will tighten them down. First set the template on the holder without any holes drilled yet. Take a look at where the template is in relationship to the stock you are going to turn and the spur center and tail stock. Smaller plugs might be mounted on the holder in a different place as a larger ones. Then mark the template and then drill the mounting holes. This might seem confusing but once you drill one in the wrong place you will see what I mean. Not all the templates will be drilled in the same location. You want to have most of the templates to be in the somewhat same location in relationship to the stock you are about to turn, so you do not have to move the whole duplicator base as much.
Last edited by ProfessorM; 03-12-2005 at 12:57 PM..
|
|
|
|
03-11-2005, 06:36 PM
|
#6
|
Uncle Remus
Join Date: Mar 2003
Location: Lakeville Ma.
Posts: 14,773
|
Template mounted on holder. Templates are made of maple.
|
|
|
|
03-11-2005, 06:37 PM
|
#7
|
Uncle Remus
Join Date: Mar 2003
Location: Lakeville Ma.
Posts: 14,773
|
Tool holder. This is the most important part of the duplicator.
|
|
|
|
03-11-2005, 06:38 PM
|
#8
|
Uncle Remus
Join Date: Mar 2003
Location: Lakeville Ma.
Posts: 14,773
|
Another view. If you are making the holder out of some light stock you might want to drill some holes in the bottomn and fill them with lead to add weight to the holder. The heavier the tool holder the better. You will get less chattering of the tool with the extra weight. It does take some getting used too, to get the so called feel of the holder. You can't just jam the tool bit into the wood or it will grab it. The tool bit is being moved by hand and you need a strong and steady hand to keep from ripping the piece out of the lathe.
Last edited by ProfessorM; 03-11-2005 at 07:33 PM..
|
|
|
|
03-11-2005, 06:41 PM
|
#9
|
Uncle Remus
Join Date: Mar 2003
Location: Lakeville Ma.
Posts: 14,773
|
Bottom of tool holder. I used a piece of plastic to keep from having aluminum on aluminum which would gall up after a while. You need to use materials that will allow the holder to slide on the plate, yet not wear down. I also put 45 degree angles on the front of the holder for clearance so you can get closer to the work piece.
|
|
|
|
03-11-2005, 06:48 PM
|
#10
|
Uncle Remus
Join Date: Mar 2003
Location: Lakeville Ma.
Posts: 14,773
|
Here is one of the critical things when you make the holder. You need to have the tool bit point, or cutting edge, to be in line up and down with the follower point. To say it another way you need to have the follower point and the tool point to be the same distance in from the same edge, say side to side not up and down. Up and down is very important also but side to side is too. That way when you apply the tool to the piece and move it back and forth they will be in unison. You will see what I mean when you turn your first piece.
Last edited by ProfessorM; 03-12-2005 at 01:02 PM..
|
|
|
|
03-11-2005, 06:51 PM
|
#11
|
Registered User
Join Date: Jul 2002
Location: Maine
Posts: 4,547
|
|
|
|
|
03-11-2005, 06:54 PM
|
#12
|
Uncle Remus
Join Date: Mar 2003
Location: Lakeville Ma.
Posts: 14,773
|
Here is probably the most critical aspect of the holder. The cutting tool and the follower point must be the same distance out from the holder, up and down. You can do this with a square. Push the follower and the tool out till the are both the same. You will need to make it so the tool bit and the follower are both adjustable, in and out, then lock them in place. When you make your tool holder you must make it so the cutting tool is on center. You need to mount your plate first. Then get a measurement from the bottom of the plate to the centerline of the lathe. I did this by measureing up to the tailstock center's point. Then compensate for the size tool you are going to use. That is why I made the tool holder's tool groove at an angle so you can adjust the tool out and it goes up too so you can get it centered. You lock in the cutting tool on center and then you bring out the follower point to the same distance and lock.
Last edited by ProfessorM; 03-12-2005 at 01:03 PM..
|
|
|
|
03-11-2005, 07:00 PM
|
#13
|
Uncle Remus
Join Date: Mar 2003
Location: Lakeville Ma.
Posts: 14,773
|
Here are the tool bits I use. They are lathe tools. I use both carbid and high speed steel, tool steel. They are 60 degree pointed tools that I sharpen to my own specs. A small radius on the tip will give a much better finish than a sharp point. They are much cheaper than the ones sold in the woodworking cataloges. The carbide tool requires a special grinding wheel but the high speed steel can be sharpened with a normal grinding wheel. When it gets dull just stone the edge man.
|
|
|
|
03-11-2005, 07:05 PM
|
#14
|
Uncle Remus
Join Date: Mar 2003
Location: Lakeville Ma.
Posts: 14,773
|
Template's are easily made by just scanning a plug you want to copy. Print out the picture. Cut along the edge. Lay the photo on your template material. Trace the picture. Cut out on bandsaw. Sand and smooth. Drill the mounting holes and you are ready to go. Fishingbumwannabe,aka Fred, told me about this method. I am also thinking about sealing the surface the tool rides on so it does not wear. I think you would have to make a real lot of plugs for it to wear though because you are really only touching the template with the follower on the final pass over the wood.
Last edited by ProfessorM; 03-12-2005 at 11:12 AM..
|
|
|
|
03-11-2005, 07:07 PM
|
#15
|
Uncle Remus
Join Date: Mar 2003
Location: Lakeville Ma.
Posts: 14,773
|
Here is the picture laid on the template material. That is an old Hawg Hunter canal plug I am going to copy. As you first start the turning process make the plug diameter larger than the finished size. Then start moving the template away until you get to the final finished size. I use a dial calipers and measure as I go. Sometimes I need to move just one side sometimes both sides of template. That is where the two sided adjustments come into play. Make sure you sneek up on it or you will be undersize and need to start again. Once you get the final size just tighten everything down and have at it.
Last edited by ProfessorM; 03-12-2005 at 12:31 PM..
|
|
|
|
03-11-2005, 07:11 PM
|
#16
|
Uncle Remus
Join Date: Mar 2003
Location: Lakeville Ma.
Posts: 14,773
|
Here are some of my assorted templates. You can also make a plug free hand on the lathe and then scan it and make up a template to produce copies of your own creation. You will probably make some changes as you use the duplicator. I have made several so far. I am sure you are sick of seeing Frank Zappa by now so that is it. If you need any more details just ask. Go for it. Paul
Last edited by ProfessorM; 03-11-2005 at 07:27 PM..
|
|
|
|
03-11-2005, 07:28 PM
|
#17
|
Registered User
Join Date: Dec 2004
Location: Delaware Co., PA
Posts: 210
|
Now thats a beautiful piece of machine work. Nice job and enjoy.
|
|
|
|
03-11-2005, 07:41 PM
|
#18
|
Registered Grandpa
Join Date: Nov 2003
Location: east coast
Posts: 8,592
|
Paul,awesome stuff.Thank you. 
How are you attaching the base plate to the lathe base?
|
" Choose Life "
|
|
|
03-11-2005, 08:11 PM
|
#19
|
Registered User
Join Date: Sep 2003
Location: Libtardia
Posts: 21,557
|
sick- you need some handlebar grips for that 
|
|
|
|
03-15-2005, 03:42 PM
|
#20
|
Boston Anglah
Join Date: Sep 2004
Location: Sitting on top of the world with my legs hangin free
Posts: 3,322
|
|
Used hard and put away dirty....
|
|
|
03-27-2005, 01:23 AM
|
#21
|
Primate
Join Date: Nov 2004
Location: Central Jersey
Posts: 106
|
I attempted to make a duplicator similar to yours and I am having a big problem with tearout. I know it is the grind on the bit because I tried the same bit in the tool holder with the same results(it's an older logan metal lathe). I tried different types of wood and it tears everything, even maple which I had the best finishes with in the past. I've turned wood on this machine before, but I can't find the bit I used and I can't remember how I ground the bit to have it work right in the first place. What's the trick to this? I tried a square bit ground to a 60 deg. point with the nose radiused slightly, a thread cutting bit, and a radiused 90 deg. bit. I tried cutting on center, above center, and below all to no avail except above seemed to be the smoothest although I could only cut .020" at a pass and this machine can do brass at that depth. I even played around with the top and side angles and not much difference. Can you suggest anything for me to try? I know it shouldn't tear the wood up this much and I'm about at my wit's end with this. 
|
|
|
|
03-27-2005, 05:56 AM
|
#22
|
Really Old & Really Grumpy
Join Date: Jun 2002
Location: not a clue
Posts: 4,860
|
I have found the half round works the best of all the different cutter's....tool steel.
|
BOAT fish do count.
|
|
|
03-27-2005, 07:36 PM
|
#23
|
Uncle Remus
Join Date: Mar 2003
Location: Lakeville Ma.
Posts: 14,773
|
Tool
I agree with Capesam that a radius bit is the best. I use a 60 degree bit too. I like a much smaller radius on the point than Capesams. I find that if I use a big radius on the tip I get a little vibration, especially if I am doing a small dia. plug or a hard material like rock maple into a needle. I too use high speed steel, 1/2 square, but also use carbid ground the same way. I add an angle on the bit, if you look at the front view, that I think makes the tool cut much cleaner. The side view, like CS's, has the much needed angle also. I have never experienced any tearout but with a sharp point the finish looks like crap which is why you need the radius on the point. Maybe you are being too aggressive with the amout of stock you are trying to remove . Maybe your RPM's are too slow but you said you did it before. Try what Capesam's and I suggested and if still can't get good results send me the bit and I will grind for you. Paul
|
|
|
|
03-11-2005, 08:31 PM
|
#24
|
Uncle Remus
Join Date: Mar 2003
Location: Lakeville Ma.
Posts: 14,773
|
I fabricated some T nuts using aluminum and some large flat head screws to be flush with the plate. They go under the lathe bed just like the T nuts for the tailstock and other lathe bolt on stuff. You can probably use any material that can be tapped so you can bolt the plate down. To bad you don't know anybody in the machine trade  . Hopefully others will chime in on how they got around this problem . Paul
Last edited by ProfessorM; 03-12-2005 at 11:06 AM..
|
|
|
|
03-11-2005, 08:32 PM
|
#25
|
Uncle Remus
Join Date: Mar 2003
Location: Lakeville Ma.
Posts: 14,773
|
Another
|
|
|
|
03-11-2005, 08:33 PM
|
#26
|
Registered Grandpa
Join Date: Nov 2003
Location: east coast
Posts: 8,592
|
"If you only knew someone in the machine business"
Would tapping the lathe base and using those allen wrench screws under each side of the lathe under the what cha call it spinner? and tailstock work,or be in the way?
|
" Choose Life "
|
|
|
03-11-2005, 09:07 PM
|
#27
|
Super Moderator
Join Date: Aug 2000
Location: Middleboro MA
Posts: 17,119
|
Sweet!
Nice job PM
|
|
|
|
03-12-2005, 08:27 AM
|
#28
|
Afterhours Custom Plugs
Join Date: Mar 2004
Location: R.I.
Posts: 8,544
|
that's one of the nicest machines i've seen, super job! btw- i miss frank 
|
|
|
|
03-12-2005, 08:40 AM
|
#29
|
Registered User
Join Date: Jan 2003
Location: Hard aground
Posts: 1,362
|
Nice Job MoonUnit 
|
|
|
|
03-12-2005, 08:42 AM
|
#30
|
Salt of the Earth
Join Date: Nov 2002
Location: Suburbia, RI
Posts: 1,025
|
Great Job PM!!!!
When the carbide tools fail, do they chip or is it just some wear on the edge? how much life are you getting out of them?
I've got a vega - was too lazy to make a duplicator myself- and have been thinking about making my own tool holder for the 35 degree cabride inserts. i know vega sells them - but they are about $80
I make my templates just about the same way, except i cut the paper very rough, then spray adhesive and stick the paper to the template, then i cut it out on the bandsaw.....makes it a bit easier to tell which one is which once you get a bunch of them.
|
|
|
|
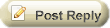 |
|
Posting Rules
|
You may not post new threads
You may not post replies
You may not post attachments
You may not edit your posts
HTML code is Off
|
|
|
All times are GMT -5. The time now is 09:26 AM.
|
| |