|
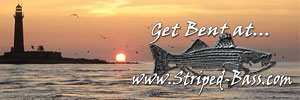 |
|
|
|
 |
|
 |
|
StriperTalk! All things Striper |
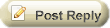 |
12-28-2014, 11:11 PM
|
#1
|
Registered User
Join Date: May 2008
Location: Chasing fat girls in the dark
Posts: 961
|
Fully Automated Eel Management system - a few questions
I'm planning to build a fully automated "eel maintenence system" to house at least 200 eels at a time for next season (yes, I know, tisk tisk). The design includes provisions to manage water temperature, change water, filter water, etc. all completely automated using PLC controls. I think I can do it for around $500 - $600.
I know some of you have set ups and was hoping you could answer a few questions.
- How many gallons of water per qty of eels?
- Optimal water temp?
- How often does the water need to be replaced? I'll be using hose water. The design includes capabilities to replace gradually, i.e. 10 gal 10 times a day or all at once, etc. Not sure if I need to let that water sit to off gas any additives like chlorine, etc.
- What do you feed them, how much, how often?
I'll share my design once I perfect it.
|
"We do not inherit the earth from our ancestors, we borrow it from our children"
|
|
|
12-29-2014, 09:54 AM
|
#2
|
Certifiable Intertidal Anguiologist
Join Date: Feb 2000
Location: Somewhere between OOB & west of Watch Hill
Posts: 35,332
|
You can never move enough clean water, 200 eels I would change 1 gallon/eel per day, temps, low 60s or cooler, tank color: dark, filter, filter, filter
Feed? Fish food? Probably be like a pit bull fight if you toss in horseshoe bits
|
~Fix the Bait~ ~Pogies Forever~
Striped Bass Fishing - All Stripers
Kobayashi Maru Election - there is no way to win.
Apocalypse is Coming:
|
|
|
12-29-2014, 10:07 AM
|
#3
|
Eels
Join Date: Jul 2004
Location: Cape Cod,MA.
Posts: 3,336
|
Not quite sure what PLC Control is but interested,if you have a water feed at the location you could install a solenoid valve to deliver water once,twice or three times within a 24hr. Time table depending on the model you get.you could get one on line or Grainger's they will be pricey thou. As for water to get exchanged I would recommend a drain port with a screen on the inside (pervent escapes)several inches from the top of the tank.
As for temperature control you could get a use Poland springs cooler to keep the water chilled bit you will have to modify the evap coil to be able to chill the water and also have an adjustable thermostat.
One other important element is to keep the water clean from the ammonia build up,any and every pet store offer a product called Ammo chips pretty cheap and many different size containers to choose from.
I use a 55 gallon plastic drum that I burried in the ground next to my foundation and under my deck this will prevent sun and thermally protection from ambiant air. At a three day heat wave water temp will be nobgreater than 70° also for food I found they don't eat.
Posted from my iPhone/Mobile device
|
|
|
|
12-29-2014, 10:39 AM
|
#4
|
Very Grumpy bay man
Join Date: Nov 2003
Location: Rhode Island
Posts: 10,876
|
I store about 2 dozen in about 25 to 30 gal of water. 4 aerators. I keep it in the back of my garage that's on the north side so no sun get in. If it's 80 to 90 degrees I change the water once a day.
As for food I buy the freeze dried Krill at the fish tank store . No sure if they eat it but I have keep eels up to a month with no ill effects. You will loose one every now and then.
|
No boat, back in the suds. 
|
|
|
12-29-2014, 12:30 PM
|
#5
|
Registered User
Join Date: Feb 2003
Location: Newtown, CT
Posts: 5,659
|
I could be wrong but I think its illegal for an individual (not a store or charter boat) to possess that many eels.
|
|
|
|
12-29-2014, 01:21 PM
|
#7
|
Registered User
Join Date: Mar 2004
Location: Marshfield, MA
Posts: 1,751
|
when is the day going to come we can't fill the bait freezer with mackeral............
|
Jon, 24' Nauset-Green Topsides, Beamie, North River. Channel 68/69. MSBA, NIBA
|
|
|
12-29-2014, 01:48 PM
|
#8
|
Registered User
Join Date: Jan 2007
Location: Reading Mass/Newburyport/merrimack river
Posts: 3,749
|
Bait dealer permits aside...
an easy way to economically keep larger quantities of eels is to purchase a live stock watering container ... they come ( or used to) in 50...100 and 200 gallon sizes... a 55 gallon drum or home made wooden one with epoxied seams work well also....use a toilet bowl flush valve for your water height control... add a bulk head fitting with ball valve ( screen the port)... each day dump 20% of the water...more if it is hot... keep a bottle of Seachem's Prime on hand and add it to the water while you fill, a cap full per 50 gallons ( of new water)...it will neutralize the chloramines and chlorine as well as heavy metals like copper that can kill fish ( the # 2 killer of captive fish...ammonia poising being #1).... for short term storage, no feeding is needed..for longer keeping pond pellets for gold fish work well and tend to contaminate the water less than meatier products... be sure to have a separate "purge" tank set up for new arrivals... as fresh caught eels will regurgitate anything in their stomachs and pollute the water ,in most cases killing the whole lot.. and trust me.. cleaning up a few hundred dead eels is no fun... been tere ..done that.. also keep a tight lid.. those slimy little buggers are the Houdini of the fish world...
I've kept up to 500 eels in a 200 gallon tub and as many as 1,000 large golden shiners in a similar set up... I still keep a fair amount of bait in a 50 gallon tub for ice fishing using this cheap easy to make system .. a good set of air stones completes the deal( be sure to clean the air stones often the eels love to lay on top of them ... eventually rendering them useless with their slime)... I have run large canister filters but if you are vigilant and change water often, you can get bye with out a biological filter ( this converts ammonia to nitrite then nitrite to nitrate).... if needed I can tell you how to make a home made canister for 1/3 the price of a store bought one..
keeping bait is easy.. it just takes a little effort. And knowledge of water chemistry..
|
A good run is better than a bad stand!
|
|
|
12-29-2014, 01:50 PM
|
#9
|
...
Join Date: Jan 2004
Location: MA/RI
Posts: 2,412
|
Design a partitioned holding tank to hold 25 eels per partition for each family member.
Posted from my iPhone/Mobile device
|
|
|
|
12-29-2014, 02:07 PM
|
#10
|
Registered User
Join Date: Dec 2003
Location: little compton ri 02837
Posts: 339
|
food for eels in captivity
Curious does anyone out there know a readily available food source for eels in a tank that they would eat? I don't want to use horseshoe 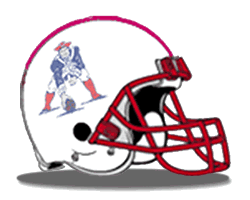 crabs. they are far better used for medical purposes, in fact they can tap them for blood with a high survival rate Its a waste to kill them for bait or to feed them to bait eels. just curious if any one has any ideas
|
|
|
|
12-29-2014, 02:22 PM
|
#11
|
Registered User
Join Date: Jan 2007
Location: Reading Mass/Newburyport/merrimack river
Posts: 3,749
|
Quote:
Originally Posted by dannyplug1
Curious does anyone out there know a readily available food source for eels in a tank that they would eat? I don't want to use horseshoe 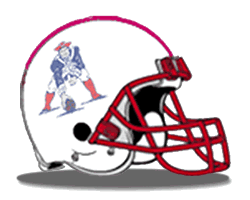 crabs. they are far better used for medical purposes, in fact they can tap them for blood with a high survival rate Its a waste to kill them for bait or to feed them to bait eels. just curious if any one has any ideas
|
per my post...pond pellets for gold fish.. besides being inexpensive.. they contain vitamins and minerals to maintain their skeletons and slime coat... the fish meal in them assures that they are consumed... they tend to pollute the water less than other meaty foods..
|
A good run is better than a bad stand!
|
|
|
12-29-2014, 02:34 PM
|
#12
|
Registered User
Join Date: Mar 2004
Location: Marshfield, MA
Posts: 1,751
|
So, WRT this new regulation......
I guess this would not apply if you are commercial fishing since this applies to recreational eel possession.
But recreationally, if you buy or trap or whatever 10 eels everyday and only use half of these and toss the left overs in your at home keep tank and weeks later have 70 at home are you in violation? It says 25 PER DAY.
|
Jon, 24' Nauset-Green Topsides, Beamie, North River. Channel 68/69. MSBA, NIBA
|
|
|
12-29-2014, 02:40 PM
|
#13
|
"Fishbucket"
Join Date: Feb 2004
Location: Bahston Hahbah
Posts: 6,588
|
•It is unlawful for any fisherman to take, possess or land more than 25 eels per day without holding a commercial fisherman permit endorsed for eels
•If an individual purchases more that 25 eels from a bait shop or dealer and is transporting eels, the individual must be able to document the purchase of eels with a receipt from the seller
As long as you have the permit you can have as many as you want.
American Eel (1)
All Jan 01 - Dec 31
9 in
No Limit
of course, Charter boats have special rules 
Last edited by thefishingfreak; 12-29-2014 at 04:30 PM..
|
|
|
|
12-29-2014, 04:53 PM
|
#14
|
Registered User
Join Date: Aug 2005
Location: Rhode Island
Posts: 258
|
I just picked up a lobster tank for next to nothing. My present tank is about 80 gallons old chest freezer airated and flushes 1 time a day automatic, twice a day during late junt thru early sept. I think the lobster tank is going to be better keeping the temp around 55 and with the biofilter. Gonna black out the glass, so we will see.
|
|
|
|
12-29-2014, 06:43 PM
|
#15
|
User
Join Date: Jun 2012
Location: Cape Cod
Posts: 5,536
|
Quote:
Originally Posted by thefishingfreak
•It is unlawful for any fisherman to take, possess or land more than 25 eels per day without holding a commercial fisherman permit endorsed for eels
•If an individual purchases more that 25 eels from a bait shop or dealer and is transporting eels, the individual must be able to document the purchase of eels with a receipt from the seller
As long as you have the permit you can have as many as you want.
American Eel (1)
All Jan 01 - Dec 31
9 in
No Limit
of course, Charter boats have special rules 
|
And if that's not enough,,, check with your local Natural Resource office,, there is most likely a town permit required also.. 
|
|
|
|
12-30-2014, 04:18 PM
|
#16
|
Registered User
Join Date: May 2010
Location: Pembroke
Posts: 3,343
|
This is MA ! No civilian should have high capacity anything...ever.
|
Does your incessant whining make you feel better? How about you just shut the hell up and suck it up? It's a fishing forum , so please just stop.
|
|
|
12-30-2014, 04:50 PM
|
#17
|
Registered User
Join Date: Oct 2005
Location: Vineyard Haven
Posts: 413
|
go sneak a peak at you local B&T set up and ask lots of questions. I couldn't imagine what the water bill would be if our changing water everyday.
|
|
|
|
12-30-2014, 06:26 PM
|
#18
|
xxx
Join Date: Oct 2003
Location: Playin' in the Dark
Posts: 2,407
|
Unless your keeping them for months, don't feed them, they'll just dirty up the water quicker. Keep the tank cool and dark and they'll just lay around not using much energy.
Posted from my iPhone/Mobile device
|
|
|
|
12-30-2014, 07:13 PM
|
#19
|
Registered User
Join Date: May 2008
Location: Chasing fat girls in the dark
Posts: 961
|
Thanks everyone. I'm going to build it on paper first and then start sourcing materials.
|
"We do not inherit the earth from our ancestors, we borrow it from our children"
|
|
|
12-31-2014, 01:39 AM
|
#20
|
Registered User
Join Date: May 2008
Location: Chasing fat girls in the dark
Posts: 961
|
Here’s the initial design on paper: Design basis – Maintain at least 100 eels for 10 days with no human interaction.
The tank will be on a slight angle so maybe the eel poop will settle near the drain valve and will be sucked out when the valve opens to let water out.
The temp probe will connect to the PLC (programmable logic controller) and be configured to activate the cooling circ pump when the temp hits 60 and shut off when the temp reaches 55.
The drain valve will be controlled by the PLC on a schedule and will be the start of a cycle. Drain opens and lets water (and poop) out until the bottom (adjustable height) float switch activates. This signals the PLC to close the drain valve, activate dispenser to add appropriate amount of water conditioner and open the fill valve until the top float switch makes. This signals the PLC to shut the fill valve. I need to build in some fail safe conditions for switch failures so as not to over flow the tank or never start the fill cycle if the lower switch doesn’t activate for switch failure or clog, etc. I can do this with maximum durations or dual switches.
Adjustments are simple: Add or delete quantity of flush cycles to the PLC logic, raise or lower the lower float switch to adjust the quantity of water replaced per flush. This should give enough flexibility to find the sweet spot between maintaining temp and water quality.
Not sure if the filter will be needed based on flush capabilities but could be the back-up if the flush cycle fails to activate = turn on filter pump.
|
"We do not inherit the earth from our ancestors, we borrow it from our children"
|
|
|
12-31-2014, 09:47 AM
|
#21
|
Registered User
Join Date: Mar 2012
Location: MASS. I miss CT
Posts: 213
|
I use a koi pond that came with the house I bought. No filter, no moving water, and no food. I was able to keep 100+ canal eels alive in mesh bags throughout the summer. The pond is about 3-4 feet deep and sticks like rotten mud. For some reason it's been working just fine and it's located in a shaded area.
|
|
|
|
12-31-2014, 10:21 AM
|
#22
|
Registered User
Join Date: Mar 2004
Location: Marshfield, MA
Posts: 1,751
|
Nice Project, I like your thinking,.....just not too convinced on the heat transfer of the refrigerator to tubing vice a direct freon to water heat exchanger or like a water cooler where the water tubing is in direct contact with the freon capiliaries. What you have there will work just don't know how efficient.
|
Jon, 24' Nauset-Green Topsides, Beamie, North River. Channel 68/69. MSBA, NIBA
|
|
|
01-03-2015, 11:00 AM
|
#23
|
Registered User
Join Date: Sep 2011
Location: Plymouth MA
Posts: 137
|
30 gallon cooler and a whisper quiet pump with air stone kept 50+ alive for a month plus at a time with 25% of the water being changed every other day.
Posted from my iPhone/Mobile device
|
|
|
|
01-07-2015, 03:56 PM
|
#24
|
Registered User
Join Date: Oct 2001
Posts: 1,990
|
Quote:
Originally Posted by lamigsb1
30 gallon cooler and a whisper quiet pump with air stone kept 50+ alive for a month plus at a time with 25% of the water being changed every other day.
Posted from my iPhone/Mobile device
|
Same here, I just added a big 3" drain valve and screen, otherwise it takes forever to empty. Seems like a lot of $ and time for something so easy to take care of.
Posted from my iPhone/Mobile device
|
Sooner or later you're going to realize just as I did that there's a difference between knowing the path and walking the path. - Morpheus
|
|
|
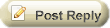 |
Posting Rules
|
You may not post new threads
You may not post replies
You may not post attachments
You may not edit your posts
HTML code is Off
|
|
|
All times are GMT -5. The time now is 11:53 PM.
|
| |